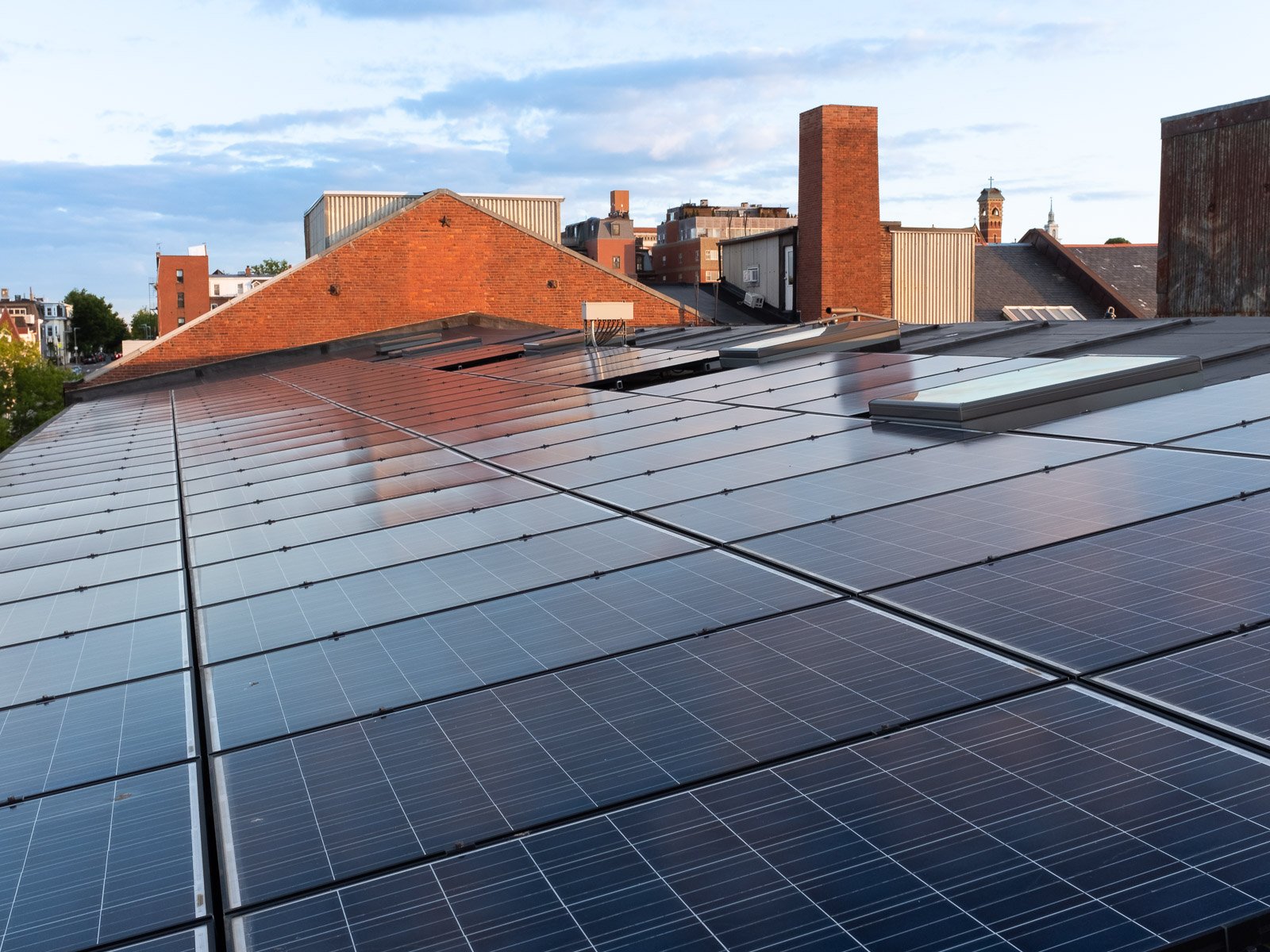
The Distillery North is one of the most energy-efficient buildings in Boston. Compared to a conventional new building, these 28 apartments use:
90% less energy for heating and cooling and
60% less total energy
The Distillery North is built and certified according to the Passive House standard, using advanced but practical methods to achieve high energy savings.
It also surpasses the LEED Platinum green building criteria.
The goal of The Distillery North is to cut carbon emissions while giving residents exceptional comfort and indoor air-quality.
Read about creating The Distillery North and the energy performance it achieves: The Distillery North Proves How Energy-efficient Multifamily Buildings Can Be
Advanced features that work
-
Better windows
Tilt-turn windows are triple-paned and tight-sealing for thermal and acoustic insulation.
-
Fresh air
Heat recovery ventilators in each unit circulate fresh, highly filtered air, with up to 95% thermal efficiency.
-
Insulation
Extensive cellulose insulation and air-tight sealing maintain interior temperatures.
-
Green power
100 solar panels atop the original factory building generate renewable energy.
Time-lapse video of The Distillery North construction
Buildings that are certified to the Passive House standard use a specific process that differs from conventional methods. The building concept is designed for energy savings from the start so each element works together. Architecture and engineering plans must be certified before construction begins, and efficiency is tested when the building is complete to verify it performs as promised.
It is essential that the structure’s exterior is free of air leaks. Before the windows and doors were cut in, the shell of The Distillery North was completed and the interior was pressurized to measure air tightness (a blower door test).
Wall cavities are filled with cellulose insulation (paper fiber) and Rockwool (melted stone spun into fiber-like material). Use of petroleum-based foam was minimized because of its greenhouse gas emissions. The orange terracotta siding tiles were chosen because they are durable, produced with less energy than brick, and don’t require painting.
Passive House Institute US (PHIUS) is one of the two main Passive House certification bodies. Thousands of buildings have now been constructed with this approach to deep energy conservation, including single-family homes, apartment buildings, affordable housing developments, schools, and even luxury skyscrapers.